Thinking Outside the Wooden Box: An Alternate Construction Method for Resilient Affordable Housing
April 05, 2023 | By Sam McGlone
Affordable housing in the United States has long been constructed utilizing lowest-cost materials and methods, resulting in low density, mid-quality, and short-lived buildings.
Traditionally, wood framed construction is the lowest cost, accommodating clients with smaller budgets, and making it an easy choice for maximizing return. However, affordable wood frame construction has structural limitations, in addition to others defined in the building code. This, coupled with the increasing cost of nominal wood framing makes it evident that the material choice for affordable housing is no longer as clear. Enter thin-shell concrete.
Thin-shell concrete is a novel construction technology that has just recently begun to establish a foothold in the United States, but has been used globally for years. The construction system uses a modularized, reusable, aluminum formwork system. It also uses lighter weight wire mesh reinforcing in lieu of traditional rebar and offers a significantly faster pour time.
The rhythmic nature of this construction system lends itself to the inherent regularity and modularity of the affordable housing market, particularly the Single Resident Occupancy (SRO) model. These projects normally have little variation in the unit typology and development groups tend to repeat the basic units. The repetitive nature of the units helps instill institutional knowledge within the facilities teams to aid in the long-term care of the projects. Because the form work is lightweight (aluminum) and can be used up to 2000 times depending on the manufacturer, the higher initial cost can be aggregated over multiple projects, thus reducing the overall investment.
While initially more carbon intensive than wood, thin-shell concrete allows for a greater density, and it can move the construction type from 5A to 1A; meaning the height of the project is no longer limited to four stories on grade or four stories above a podium. For example, a 175-unit complex with a combination of ground floor units, a modest resident services program, a small office or retail component and associated surface parking would usually require approximately one city block. Using a thin-shell system, the same density can easily be achieved in half a city block. Often, non-profit organizations and developers focused on this market have land that has been either donated to them or that can be attained with limited funding. Acquiring an entire city block is a difficult and costly proposition, but the increased density lowers the land premium for the developer, allowing them to deliver the same quantity and quality of units while lowering soft costs.
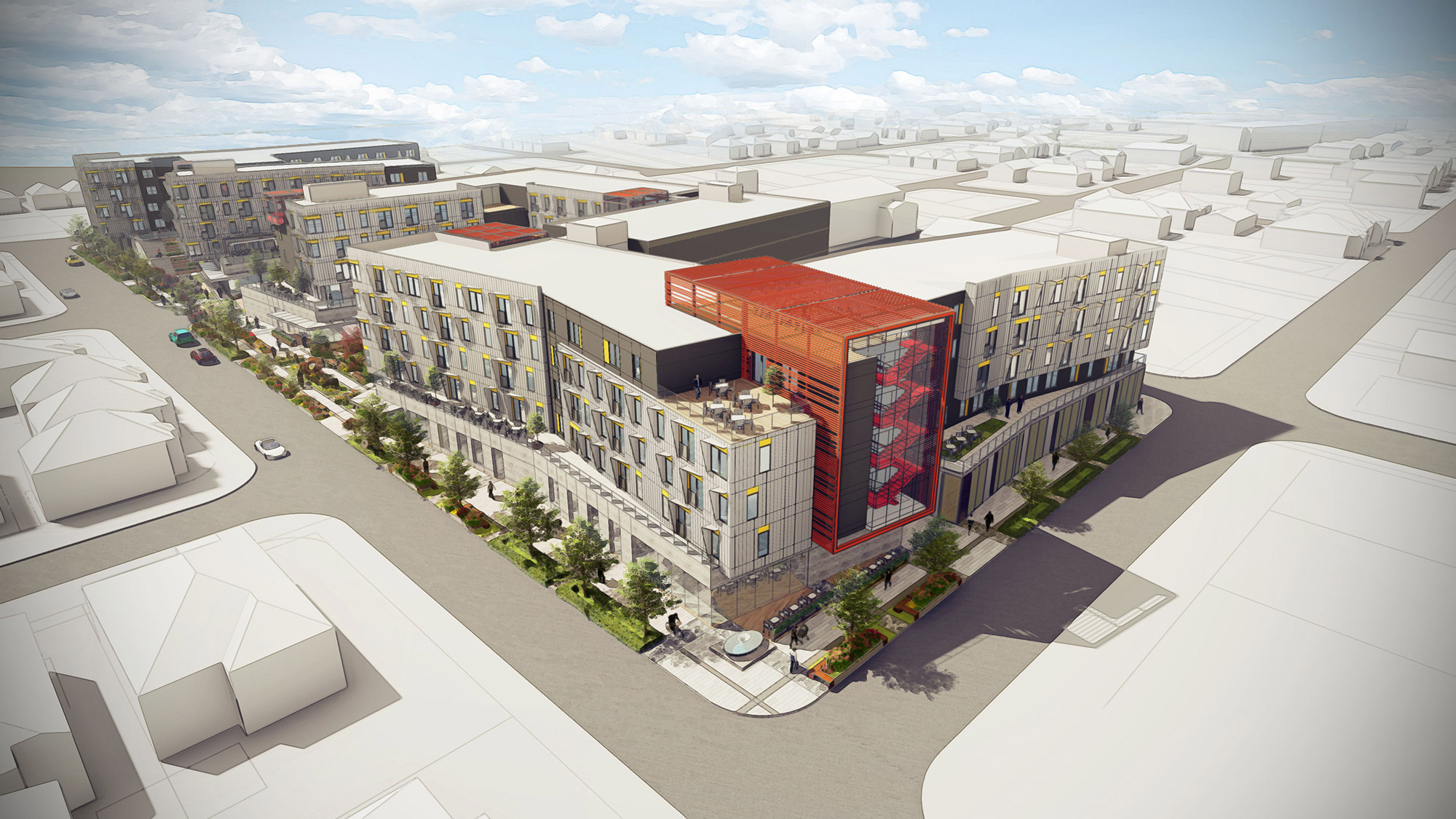
Thin-shell concrete can also improve the long-term resiliency and adaptability of the affordable housing market. As currently constructed, wood framed buildings have a limited lifespan, particularly those in wet and humid climates. In any project, water infiltration is a serious problem, however it is magnified in a wood framed construction. Eventually the wood will rot and must be replaced, which is a complicated proposition in a loadbearing wood structure. Conversely, if the structure were made of concrete with wood exterior infill walls, the building would feel limited impact should the wood need to be replaced in the future. Additionally, the same logic could be applied to a metal stud infill wall.
In most large-scale projects, concrete will last beyond 100 years if it is properly cared for and maintained. Moreover, a building designed on the correct module would allow for the structure to be adapted, should the institutional goals of the project change over time.
A standard SRO unit, not dissimilar from a hotel unit, is constructed on a 12’-6” module. The typical residential unit in a market rate apartment is based on a 25’ module. If laid out correctly, a building based around an SRO scheme could be adapted into a 1 or 2-bedroom scheme by creating an opening between two or three units. This can be done because thin-shell concrete uses a wire mesh system of reinforcing rather than traditional rebar. In collaboration with the client, we can plan to create opportunities for connection between units for future adaptation.
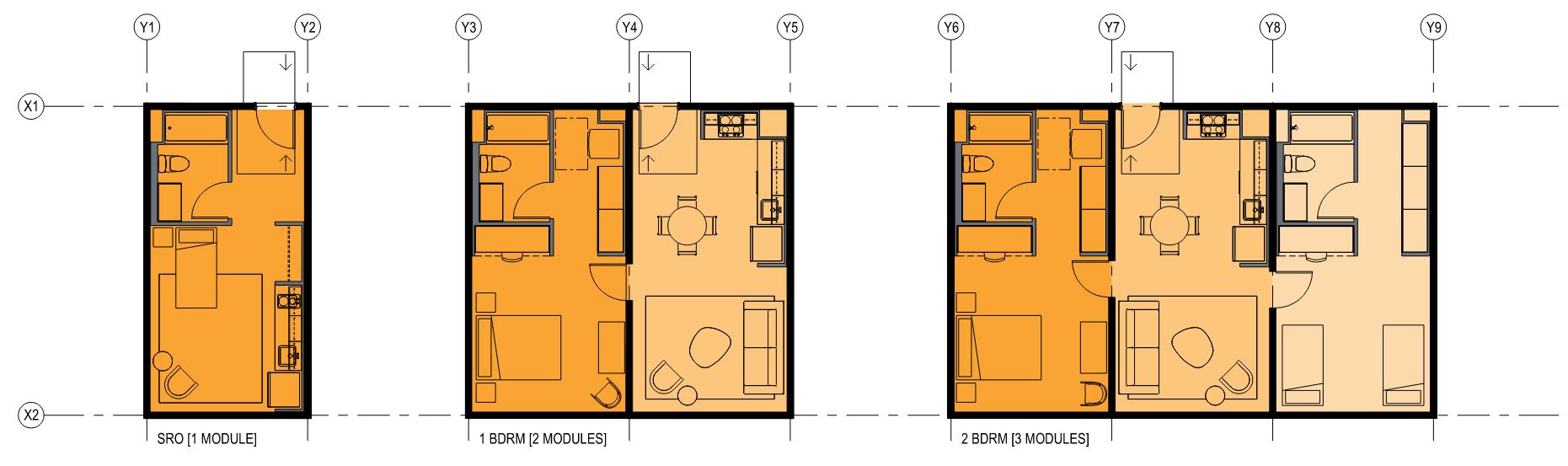
The reverse is true as well: because the module remains the same, and there is no unique form work or structural gymnastics required in the unit stacking. The building could be designed as SRO units serving individual tenants and could then be converted to 1- and 2-bedroom family units, should the need arise.
As we push for ever more sustainable building practices and building technologies, it’s important to remember that the reuse of a building is vastly more sustainable than demolishing and replacing the entirety of a building every 30 to 35 years. Utilizing this construction technology allows us to quite literally design the reuse into the building in the present, for the future.
Quality, affordable housing is and will continue to be a need in our local, regional, and global communities as cities grow and evolve in the coming decades. Our solutions to those challenges need to grow and evolve as well. Ultimately, thin-shell concrete has the potential to aid in improving the efficiency, adaptability, resiliency, and long-term viability of affordable housing.